扣件參數化設計及成形負荷快速評估系統
摘要
本文提出扣件多道次製程設計及成形負荷預估方法,以快速評估產品成形負荷並提供成形曲線以做為調模參考。經由上界限法與厚壁圓環理論建立扣件成形負荷及模具應力預測,依據不同螺栓類產品幾何參數,自動產生標準成形製程並比較各道次負荷,由模具應力預估進行應力環最佳干涉量設計。以M6螺栓鍛造為例,經由FEM分析比較負荷估算誤差皆小於10%,並可快速預測各道次成形負荷及最佳應力環設計參數,可提供適當的機台選用參考,本系統可提供設計工程師快速評估製程設計,累積成形設計經驗,縮短設計的時程,提升產品開發速度。
Methods of the multi-pass forming process design and forging load prediction were proposed to predict the forming load faster and provides load curve as die adjustment for the fastener production industry. The forming load requirement and the die stress analysis were generated via the upper bound method and the thick-walled cylinder theory, respectively. The standard forming process and load predictions were generated automatically according to the specified bolt dimensions, and the optimum interference amount of the compression ring was calculated. A M6 bolt was taken to present the proposed system. The comparison of the load predictions with the FEM simulation results showed 10% deviation which is good enough for industry applications to estimate load requirement and the compression ring design. The proposed methods and the developed system were capable of helping engineers to estimate new process design, gather forming experience, shorten lead time of process design, and cut the product development time consumption.
關鍵詞(Keywords)
快速評估系統、上界限法、厚壁園環理論
Fast evaluate system, Upper bound theory, Thick wall cylinders theory
前言
螺栓製程為一種連續的螺栓成形方式,一般分為下料、頭部預成形、頭部成形等依成品增減道次數,利用盤元或棒材為基材,先將金屬切斷,並運用各道次沖頭衝壓,將材料擠至模具內,再進行熱處理、電鍍等表面工序。
於成形模擬、上界限法、應力環設計、快速評估的相關文獻: 1.成形模擬: Sheth等人[1]運用FEM與理論的方式進行鍛造負荷預估,再將結果與實驗進行比較,FEM運用LS-DYNA預估鍛造負荷,理論則運用切片法計算,最後理論與FEM相較下理論成形負荷預估較FEM高,但仍然在可接受範圍內。Sheu 等人[2]使用二維、三維有限元素分析及形狀複雜度預測在剖面上材料的流動以及鍛件的變形細節。2.上界限法分析: C. H. Lee等人[3]推導出用於考慮鼓脹量的圓環壓縮試驗速度場。R.Ebrahimi 等人[4]提出用於有鼓脹量的圓柱壓縮試驗上界限分析,並推導出在各式摩擦條件下所對應的鼓脹量最佳化。3.應力環設計: 應力環設計常使用厚壁圓環理論為基礎預估應力環干涉面直徑與干涉量[5]。一般透過Tresca降伏準則可預估出模具的最大承受內壓力,預估適當的干涉面直徑與干涉比,作為設計應力環之依據[6]。Frater[7]以厚壁圓環理論與有線元素軟體模擬的結果作比較,研究結果顯示,在平面應力狀態時可以準確地預測模具應力狀態。4.快速評估系統: Gangopadhyay等人[8]開發基於電腦軟體運算與模糊理論的專家系統來預測鍛造負荷與軸向應力的趨勢,測試的結果與現有文獻中的實驗相比較後結果相當。Donzella等人[9]考慮室溫與鍛件、模具的彈性與彈塑性後對拔模力進行研究,並基於上述條件建立一拔模力理論模型與實驗比對,結果顯示僅有7%的誤差。Myung等人[10]藉由機械零件中的參數模型建置以及專家系統設計出整合系統,此系統有著專家系統的外部運算,再將設計資料庫以及參數模型作為核心。
本文以六角凸緣螺栓作為研究對象,以螺栓成形負荷、模具應力預估、應力環設計作為研究目的,進行各道次螺栓設計及理論解模型建立。
螺絲產品、成形工法參數化設計
- 產品幾何
本研究產品為具凸緣之六角螺栓,其尺寸為M6x20.40 mm,六角對邊寬度9.70 mm,凸緣直徑14.10 mm,六角頭端和凸緣高度合6.30 mm,螺栓直徑6 mm及端部長度20.40 mm,產品設計具與規格如圖1所示。
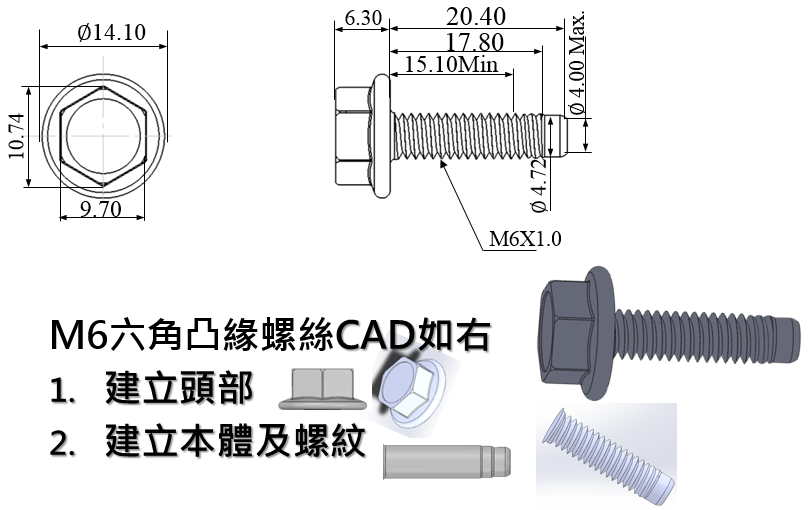
圖1 產品尺寸與規格
- 道次設計
由圖1將載具進行各道次鍛胚預成形設計,分為:(1) 下料 (2)頭部預成形 (3)頭部成形 (4)頭部六角成形 (5) 凸緣成形,等共五個道次,如圖2所示。再以體積不變(1015.97 mm3)進行設計,模具使用標準模具外徑進行設計,模擬過程中忽略下料步驟。每道次過模間隙0.01(mm)。
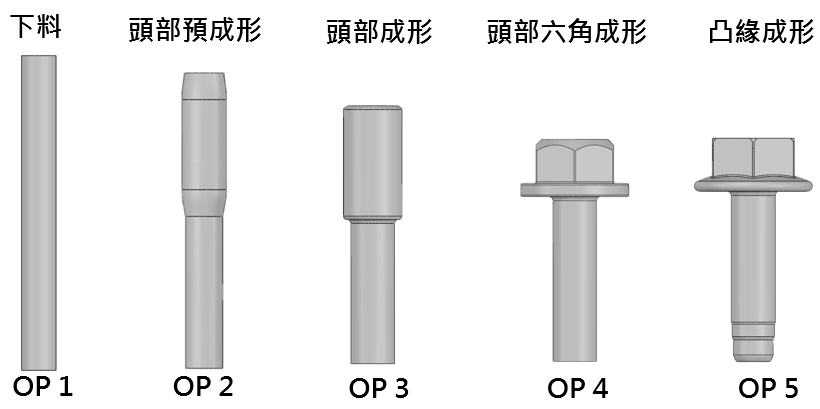
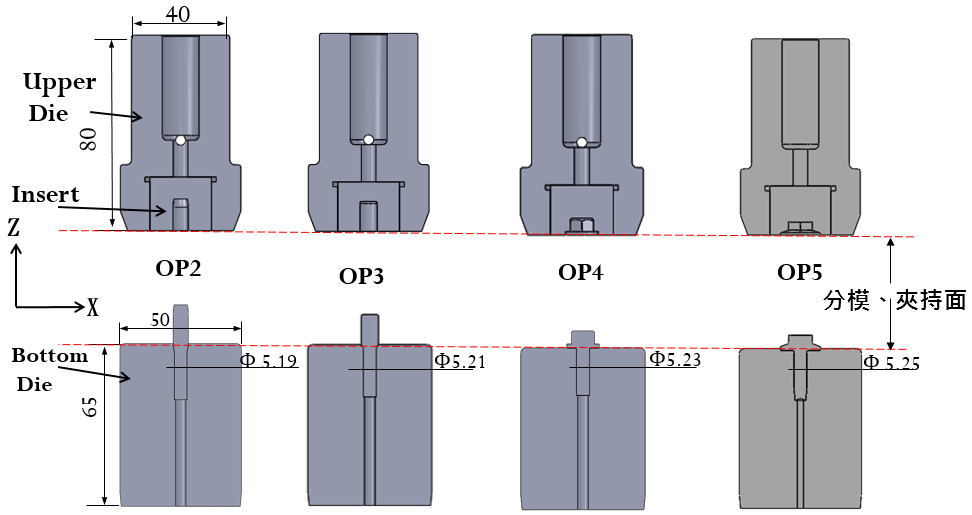
圖2 螺栓成形道次設計與模具剖面圖
- 參數化設計
以預成形胚料、母模為例,胚料置於母模內,兩者特徵關係為C=A+B C=胚料放置深度,A=胚料圓角,B=胚料棒端長度,20.1=0.4+19.7。由此可建立產品之數學關係式,再藉由設計表單建立鍛胚與模具幾何關係資料庫即可達到修改鍛胚,模具幾何自動修正之參數化設計效益。如圖3所示。
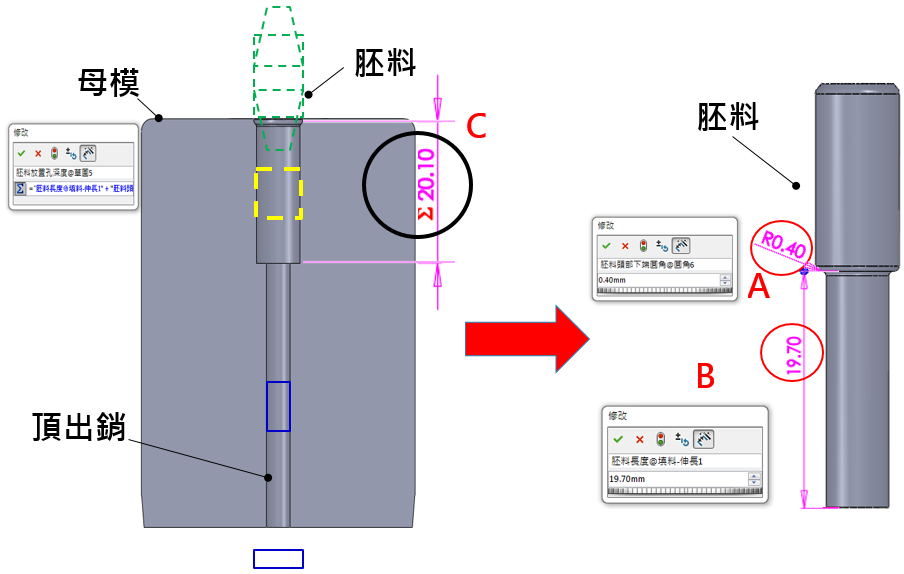
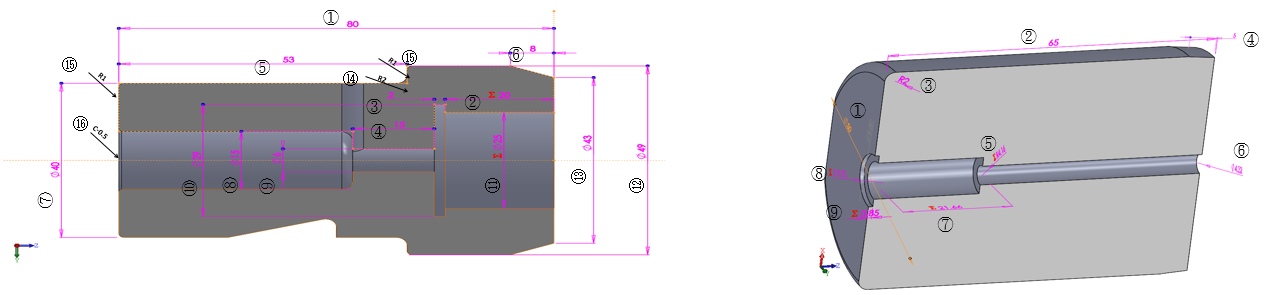
圖3 建立鍛胚與模具數學關係式與參數資料庫
扣件快速評估系統
本研究將以上界限法(UBM)發展鍛造成形負荷預估理論解,以厚壁圓環理論[5]發展應力環設計模型,其目的為預測成形負荷以做為模具設計及選用適當的生產設備。
- 圓柱壓縮
本研究建構一考慮鼓脹量(bulging)之上界限法模型,用於分析考慮鼓脹材料壓縮產生的負荷,分析模型示意圖與符號說明如圖 4所示。經推導後圓柱壓縮成形力預估模型如表1所列
…本文未結束
更完整的內容 歡迎訂購 2019年12月號 441期
機械工業雜誌‧每期240元‧一年12期2400元
我要訂購