微量切削熱溫升偵測技術應用於車削加工刀具定位
摘要:常見車削刀具定位可透過目測觀察切屑生成判定,作為依據判定刀尖與工件接觸用於達成低精度定位,或是透過刀具設定測頭、量刀臂等量測設備達成高精度定位,但量測設備價格高且需專業人員安裝校正,若全廠每台設備都要配置,是很大的成本負擔。本文的車削刀具定位技術,是基於切削過程產生熱能的物理現象,利用控制器在待測定軸進行精準移動並在其正交軸進行切削,同時搭配熱影像感測器進行切削區域的熱溫升偵測作為刀尖與工件接觸的判定依據,最佳定位精度為控制器最小移動量。在本技術中,熱影像感測器採用便攜式設計,一般使用者可自行安裝校正,並且輕易的移至其它機台使用,具備低設備成本、低使用門檻、高定位精度的優勢。
Abstract:Typically, turning tool length measurement can be done by observing the cutting chips when the tooltip contacts the workpiece in low precision, or using measuring equipment like tool setting probe or tool setting arms in high precision. But measuring equipment is expensive and has to be installed and calibrated with experts. It will be a huge cost burden to equip measuring equipment in all machines in the factory. The turning tool length measurement Technology in this article is based on the physical phenomenon that the machining process generates heat. Moving the axis to be measured precisely with the CNC controller and executing the machining process on the orthogonal axis. Judging the contact between the tooltip and workpiece with the temperature rising signal in the machining region along with the thermal image sensor. The optimal measurement precision is equal to the minimum movement of the CNC controller. The thermal image sensor is designed with a portable style in this technology. User can install/calibrate equipment easily and reinstall it on other machines, and it has the advantage of low equipment cost, low threshold for use, and high measurement precision.
關鍵詞:刀具定位、熱溫升、微量切削
Keywords:Tool length measurement, Temperature rising signal, Micro machining
前言
金屬切削產業中,刀具資源管理及工件產出品質是產線管理者的重點關注項目。因此在加工前進行刀具定位及工件定位、加工中/後需進行刀具磨耗補正、加工後需進行工件公差檢查。一般而言,在自動化程度較低的產線,刀具定位由技術人員在換刀完成後,以人工手動搭配目測的方式進行定位,後續由操作人員進行量產加工,產出的工件則抽樣以手動進行關鍵尺寸量測並依工件誤差進行刀具磨耗補正。人工操作項目較多的情況下,容易導致工件公差較大、人員工時較高、機台稼動率較低的情況。
為解決上述問題,需提升產線自動化程度,例如導入刀具設定測頭[1]用於進行刀具定位、導入接觸式觸發探測頭用於進行工件尺寸量測且透過加工流程整合延伸進行公差檢查及刀具磨耗補正。但單一量測設備價格動輒20萬元以上,且安裝及校正都需要專業人員處理,資本額較小的業者常因成本考量而未導入,無法獲得自動化程度提高帶來的益處。
本文為提升產線自動化,針對刀具定位提出新的量測方法。利用金屬切削時產生熱能且造成溫度上升的物理現象,使用熱影像感測器並結合控制器精準移動,偵測測定路徑上刀尖在切削過程中出現的熱溫升[2],用以判定此時刀尖與工件接觸且正在進行微量切削而完成自動定位設定。
微量切削熱溫升偵測技術研究
1.加工環境配置
圖1為加工環境配置,X, Z, C三軸小型車銑複合機台,刀塔可安裝8把車削刀具及1把銑削刀具,搭配工研院智機中心車床控制器,控制器最小移動量為1 μm。熱影像感測器採用FLIR Lepton 3.5 [3],有效像素160 x 120,熱靈敏度0.05°C,影像幀率8.7 Hz。工件為直徑3 cm 鐵製圓柱型棒材。熱影像感測器安裝於機台內部,鏡頭對準刀尖與工件接觸的加工區域,距離35 cm (熱影像感測器有效距離約30-150 cm)。
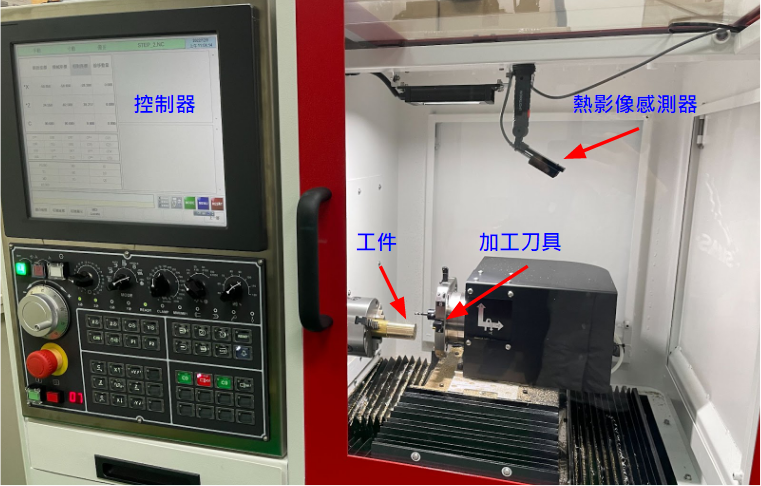
圖1 微量切削熱溫升偵測加工環境配置
2.熱影像感測器安裝校正
進行熱溫升偵測前,需先安裝及校正熱影像感測器。圖2(a),在加工區域清空無外物情況下,均溫為25.24°C、最低溫24.29°C、最高溫27.41°C。進行校正前,需先確認機台為完全靜止且待機的安全情況,如圖2(b),均溫為26.26°C、最低溫24.29°C、最高溫32.74°C,可見手指靠近加工位置的影像,確認影像範圍可完整涵蓋加工區域,且刀尖與工件接觸位置不受遮避。由於後續是透過切削過程中相對溫度變化資訊進行偵測,不需對熱影像感測器進行靈敏度的精準校正,且搭配磁吸式底座,具備安裝位置彈性的優點,一般使用者可在短時間內完成安裝校正。
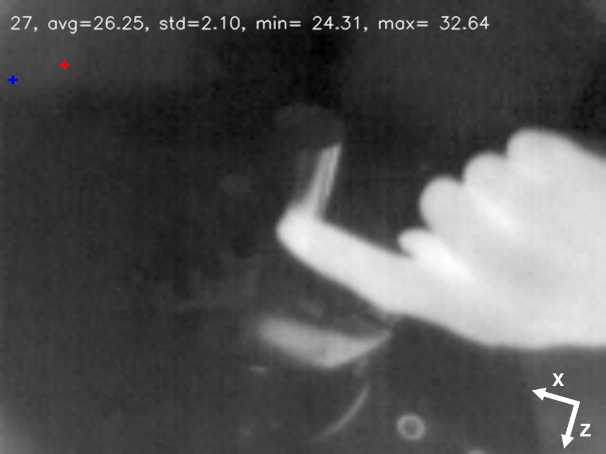
(a) (b)
圖2 熱影像感測器安裝校正加工區域熱影像 (a)無外物 (b)手指靠近工件
3.切削熱溫升偵測
切削條件設定,工件為鐵,直徑3 cm,加工參數S2000 F0.5, X軸切削深度5 μm,刀尖沿著Z軸移動進行切削。熱影像偵測及統計分析資訊如圖3所示。加工區域平均溫度為24.64°C、溫度標準差為 0.28°C、最低溫23.84°C、最高溫26.93°C。透過追蹤熱影像陣列中每一個位置的溫度變化,可獨立分析每一個熱影像點的平均溫差與目前溫度的差值即為熱溫升。
…本文未結束
更完整的內容 歡迎訂購 2023年3月號 480期
機械工業雜誌‧每期240元‧一年12期2400元
我要訂購